Past and Present
Bio-Energy is the general term for energy derived from materials such as wood, straw or animal wastes, which were living matter relatively recently - in contrast with fossil fuels. Such materials can be burnt directly to produce heat or power, but can also be converted into bio-fuels. Charcoal and bio-diesel, for example, are bio-fuels made from wood and plant seeds respectively.

Until recent times, the history of fuels was essentially the history of biofuels. Although there is evidence of coal-burning as early as 3000 years ago, its contribution remained relatively small until about 200 years ago. Indeed, bio-energy was still dominant in many areas of life well into the industrial revolution, with wood for heat, tallow candles made from animal fats fro light, and grasses as "fuel" for the only means of transport - the horse.
The move from bio-fuel to fossil fuel was a key feature of the industrial revolution. For many countries, the high temperatures needed for iron smelting could be achieved only in furnaces using charcoal. The impurities and variable nature of coal made it unsuitable for smelting, and attempts to reduce it to a type of charcoal had little success initially. But in the early 1700s, an effective "coal charcoal" was produced, and within a few decades, this new fuel, now called coke, was replacing charcoal throughout the growing industrial sector.
By the end of the nineteenth century, coal was dominant in the world's industrialized countries. The twentieth century saw the rise of oil and natural gas, but it is worth mentioning that coal consumption also increased five -fold between 1900 and 2000.
Will the twenty-first century see the reverse process namely from coal back to wood? Could Bio-fuels completely replace fossil fuels? Theoretically it is possible!

Bio Energy Sources
The two main sources of bio-energy are the purpose-grown Energy
crops and Wastes, the otherwise unwanted
products of human activities.

Energy Crops
The term energy crop is used in the widest sense, to include any
plants that are grown specifically for use as fuel or for conversion
into other bio-fuels. Includes, for instance, wood for burning,
plants for fermenting to ethanol and crops whose seeds are particularly
rich in oils (but not of course those that are grown primarily for
food).
Energy Crops have attracted increasing attention in recent years,
for several different reasons namely:
- The need for alternatives to fossil fuels, to reduce net CO2
emissions
- The search for indigenous alternatives to imported oil
- The problem of surplus agricultural land
Energy Crops can be divided up in to two headings Woody crops and
Agricultural crops
WOODY CROPS
In modified conventional forestry, whilst energy is still not the
main product, it is part of the plan. Coniferous trees are planted
at higher than usual density and vigorously thinned after a few
years, using integrated harvesting techniques to produce chipped
wood. The remaining trees grow to maturity in the normal way. There
have been trials of this system, but the main developments in recent
years have been with woody crops planted and harvested entirely
for energy production.
AGRICULTURAL CROPS
Globally the most grown crops for bio-energy purposes are sugar,
cane and maize. Both are C4 crops, with the high yields needed for
a favourable energy balance. The main interest lies in their seeds,
which can be converted to a diesel substitute, known as bio-diesel.
Wastes
There are two main types of wastes. The wastes arising direct from
uses of biomass for example forestry, agriculture and animal husbandry.
Then there’s the household, or more generally, municipal wastes
including the specific wastes associated with industrial processes.
WOOD RESIDUES
Operations such as plantations and trimming felled trees generate
large volume forestry residues. They are often left to rot on site.
Solid biomass, mainly forestry residues, fuels some 6% of Austria’s
generating capacity which two thirds of it in a CHP plant. The investment
required for the harvesting and processing machinery means that
the resource is unlikely to become economically viable until a market
for wood is fully established.
TEMPERATE CROP WASTES
World-wide residues from wheat and maize, the two main temperate
cereal crops, amount to more than a billion tonnes per year, with
an estimated energy content of 15-20 EJ. They have uses as bedding,
feed, etc. but in major cereal-growing regions more than half may
remain unused. In East Anglia in the UK about 80% of the nearly
2 million tonnes of straw produced annually is surplus to agricultural
requirements. The UK market for straw-burning systems for space
heating has been relatively slow to develop.
TROPICAL CROP WASTES
The total energy content of the annual residues of the world’s
two main tropical food crops, sugar and rice, is estimated as about
18 EJ - similar to the total for temperate crops. In this
case, however, significant quantities are already being used as
fuels. Bagasse, the fibrous residue of sugar cane, is used in sugar
factories as a fuel for raising steam, and to produce electricity
for use in the plant. Rice husks are among the most common agricultural
residues in the world, accounting for about one-fifth of unmilled
rice dry weight.
ANIMAL WASTES
Animal manure can be a major source of greenhouse gases. It is estimated,
for instance, to account for 10% of methane emissions in the USA.
Sewage sludge can be treated by anaerobic digestion. By the mid-1994,
26 projects with a total generating capacity of 33MW were supplying
electricity under the NFFO scheme, but recent years have seen no
new projects [Source: Renewable Energy, “Power for a sustainable
Future”, Second Edition, Oxford]. Poultry litter, a mixture
of chicken droppings and material such as straw, wood shavings etc.
has an energy content in the range of 9-15GJ/t depending on its
moisture.
MUNICIPLE SOLID WASTE
The average household in the world’s industrialized countries
generates rather more than a tonne of solid waste per year, with
an energy content of about 9 GJ per tonne. It appears therefore
that the average UK household could in principle supply one tenth
of its total annual energy consumption of about 90GJ from its own
wastes. In practice there is also three main ways in which Municipal
Solid Waste (MSW) is treated at present:
- Disposal in landfills
- Combustion
- Disposal in anaerobic digesters
LANDFILL GAS
A
large proportion of municipal solid waste is biological material
and its disposal in deep landfills furnishes suitable conditions
for anaerobic digestion. It was known for decades that landfill
sites produced methane, and systems were fitted to burn it off safely,
but the idea of using this Landfill Gas (LFG) developed only in
the 1970’s. The digestion in a landfill takes place over years,
rather than weeks of “wet” systems. In developing a
site, each area is covered with a layer of impervious material after
it is filled, and the gas is collected by an array of interconnected
perforated pipes at depths of up to 20m in the refuse. In a large
well established landfill there can be several kilometres of pipes,
with as much as1000 m3 per hour of gas being pumped out. In theory,
the lifetime yield per tonne of wastes in a good site should lie
in the range 150-300 m3 of gas, with between 50% and 60% by volume
of methane, which suggests a total energy of 5-6 GJ per tonne of
refuse. In practice, at the average UK gas extraction rate, the
heat energy output per tonne of wastes (as collected) is rather
less than 2 GJ, but yields are extremely variable and often unpredictable
- a factor that tends to deter potential investors.
The
gas may be used directly to fire kiln, furnaces or boilers, but
there are rarely enough large users close to a landfill site, and
the output is increasingly used to generate electricity for local
use or for sale. The generators are driven either by large internal
combustion engines or by gas turbines. Assuming a gas-to-electricity
energy efficiency of perhaps 35%, this brings the overall energy
efficiency of the system below 10%. A site containing a million
tonnes of MSW might support an electrical capacity of perhaps 2
MW over a 15-20 year generating lifetime. Despite the low energy
conversion efficiency, LFG plants have been amongst the most financially
attractive of the systems receiving contracts under the NFFO scheme,
with an annual electrical output in 2002 of some 2700GHh from an
installed capacity of about 400 MW.
An
example of the cost calculation that REH follows is:
[Source ETSU 1999]. For a site large enough to support 2 MW of generating
capacity over an operating life of 15 years with an average load
factor of 88%. The following calculation assumes a discount rate
of 8 %.
Financial Data:
Plant cost: £750 per kW
O&M costs: 1 p kW/h
Discount rate: 8%
There are 8760 hours in a year, so with 88% load factor, the 2 MW
plant will generate:
2000 x 8760 x 0.88 = 15.42 million kWh per year. Say for example
the repayment on £1000 at 8 % over 15 years is £117.
The total plant cost is £ 1 500 000, so the total annual repayment
is: 1500 x £ 117 = £ 175 000 = 17.55 million pence per
year. Expressed as a cost per kWh of output, this is 17.55 / 15.42
= 1.14 p kW/h. Adding the O&M costs gives a final electricity
unit cost of 2.14 p per kWh.

Combustion of Solid Bio Mass
Most biomass is initially solid and it can be burnt in this form to produce heat for use in situ or at not too great a distance. It may firsts require relatively simple physical processing, involving sorting, chipping, compressing and/or air-drying. Alternatively, the biomass can be upgraded by chemical or biological processes to produce gaseous or liquid fuels.

COMBUSTION OF WOOD AND CROP RESIDUES
Boiling a pan of water over a wood fire is a simple process. Unfortunately, it is also very inefficient: For example [Source: Renewable Energy, Power for a sustainable Future, Second Edition] How much wood is needed to bring one litre of water to the boil?
Data
Specific heat capacity of water = 4200 J Kg-1 K-1
Mass of 1 litre of water = 1 kg
Heat value of wood = 15 MJ kg-1
Density of Wood = 600 kg m-3
1 cubic centimetre (1 cm3 = 10-6 m3)
Calculation
Heat energy needed to heat 1 litre of water from 20 °C to 100 °C = 80 x 4200 J = 336 kJ
Heat energy released in burning 1 cm3 of wood = 15 x 600 x 10-6 MJ = 9.0 kJ
Therefore: Volume of wood required = 336 / 9.0 = 37 cm3
Conclusion
Experience suggests that on an open fire much more than two thin 20 cm sticks would be
needed. But a well-designed stove using small pieces of wood could boil the water with
as little as four times this “input” – an efficiency of 25%
Wood burning produces a wide range of pollutants, and the past few decades have seen
many programmes in developing countries for the design and dissemination of improved
stoves.
CHARCOAL
Charcoal is traditionally produced in the forests where the wood is cut. The “kiln”, consisting of stacked wood covered with an earth layer, is allowed to smoulder for a few days in the near absence of air, typically at 300 – 500 °C, a process called pyrolysis. The volatile matter is driven off, leaving the charcoal, the “char” component. Charcoal is almost pure carbon, with about twice the energy density of the original wood and burning at a much higher temperature, so it is much easier to design a simple and efficient stove for use with this high quality fuel.
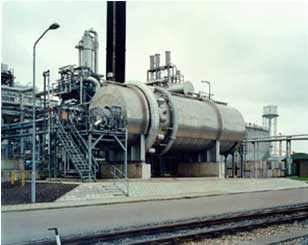
[Source of picture: Reference from Duiker Combustion Engineers] |
COMBUSTION OF MUNICIPAL SOLID WASTES
In many countries in continental Europe and elsewhere, refuse incineration with heat recovery, or Energy-from-Waste (EfW) is an important means of waste disposal. The heat may be used directly for district heating, or for power production (often in CHP plant). The inert ash can be used as hardcore. Countries with successful recycling and composting programs have often seen parallel growth in EfW, which accounts for 30-60% of MSW disposal in most West European countries. World installed capacity is over 3 GW, about half of it in Europe. EfW is becoming financially attractive in large cities in Britain because of the shortage of suitable landfill sites and high cost of transporting wastes to distant sites. Encouraged by support under the NFFO scheme, UK capacity
tripled during the 1990s, and all MSW combustion plants in the UK now make use of their heat output. A state of the art incinerator has been built on the Isle of Man. REH had no involvement with this project and wasn’t established yet. It is also known as the 'Energy-from-Waste Plant'. It reduces the amount of waste burried at landfill sites in the North of the Island, namely Point of Ayre, whilst producing electricity for the island. The plant can deal with all the burnable waste produced by the island everyday.

Production of Gaseous fuels from Bio Mass
There are several reasons for production of gaseous fuels from biomass. The result is a more versatile fuel, suitable not only for burning but for use in internal combustion engines or gas turbines. It is easier to transport, and if undesirable pollutants and inert matter are removed during processing, it will be cleaner. It offers a route to electric power that could be more efficient than the direct combustion of biomass in a conventional power station. And finally, gasification under suitable conditions can produce synthesis gas, a mixture of carbon monoxide and hydrogen from which almost any hydrocarbon, synthetic petrol, or even pure hydrogen can be made.

ANAEROBIC DIGESTION
Biogas and landfill gas is forms of anaerobic digestion of wastes. In landfill’s case the digester is the landfill itself and the operator has only limited control of the processes. The digestion of “wet wastes” is quite different. The feedstock, dung or sewage, is converted to a slurry with up to 95% water, and fed into a purpose-built digester whose temperature can be controlled. The process of anaerobic digestion is complex, but it appears that bacteria break down the organic material into sugars and then into various acids which are decomposed to produce the final gas, leaving a residue whose composition depends on the systems and the original feedstock. The biogas produced by a digester can be used to produce heat or electric power – or in many cases both. A Danish government programme investigating the economics of anaerobic digestion concluded after a six-year trial that a large-scale biogas plant could be profitable in three realistic conditions were met:
- the plant is operated in combined heat and power mode
- the gas is sold at a price comparable to that of natural gas
- credit is given for the disposal of other wastes
ANAEROBIC DIGESTERS FOR MSW
As an alternative to recovery of biogas from landfills, MSW can be subjected to more carefully controlled processing in the type of large digester described above. Under these conditions gas yields are much higher and digestion is complete within matter of weeks rather than years. An advantage over landfill is that these digesters can be that these digesters can be closer to urban areas, reducing transport costs. They also require less land, but do need higher capital investment and processing costs which is a disincentive.
GASIFICATION
Gasifiers are used for gasification. Gasification is not a new process. “Coal gas” the product of coal gasification was widely used in the UK for many decades and “wood gas” was used for heating lighting and even vehicle fuel. Both were superseded by natural gas although wood gasification reappeared during the coal shortages of World War 2. In contrast with anaerobic digestion of waste, gasification is used for chemical processes by which gaseous fuel is produced from a solid fuel (Wood chips, agricultural residues, saw dust or waste). This process is done by adding hot steam and oxygen with the solid fuel. This results into a mixture of combustible components (mainly carbon monoxide and hydrogen, with some methane, higher hydrocarbons and condensable tars) together with carbon dioxide and water. The gasification reaction does not occur easily in which the operating temperature and atmospheric pressures of the gasifier vary in a wide range. It is therefore essential to have the correct gasifier. If the output from a biomass gasifier can be cleaned and used to run the gas turbine, the possibility arises of a self-contained biomass integrated gasification combined cycle (BIGCC) system, for local power generation.
Basic Process:
There are many different designs of modern gasifiers, but essentially one basic process which is hot steam and oxygen interacting with the solid fuel
Gasification Reaction:
Operating temperature vary from 100 ºC – 1000 ºC
Pressure: 1atmosphere – 30 x atmosphere
If air is used rather then pure oxygen, nitrogen will be present and the energy content of the resulting gas would only be 3-5 MJ/m3, about a tenth of natural gas. The additional cost of the oxygen plant makes this more economic viable with large systems.
Conversion Efficiency:
Conversion efficiency from the energy of the solid fuel to that of the resulting gas varies widely, from as little as 40% in relatively simple systems to 70% or more in the most sophisticated plants.
The Biomass CHP system, with emphasis on Downdraft Gasifiers:
System’s like these converts prepared fuel into producer gas. Unlike other gasifiers it does not require additional gasses/diesel, the combustion engine starts & runs on producer gas.
Combined Heat and Power (CHP) system
Process
- Uses downdraft gasifiers to turn fuel into a combustible gas
- The gas is then filtered to remove tars and dust.
- The gas is then cooled and fed to a spark an ignition engine
- Then used for heat and power.
Fuels normally accepted
Softwoods: [spruce, pine, willow]
Hardwoods: [beech, oak, poplar]
Industrial wastes: [palletwood pieces and furniture off cuts]
Size of typical plant
To generate 250 kW > Area:10mx15m ; Height: 4m
Maintenance
Gasification systems are normally unmanned and work automatically. One person is normally required to deal with handling of the biomass, to move materials from a reception area to a biomass dryer. A dumper truck or digger and shovel could be used. Dried materials would then be stored to provide a “buffer” of material of 2-3 days [12-18t] to feed the gasifier. The gasification system is automatic and can be unmanned.
Performance
For each 250 kg of prepared biomass, this will give approximately 250 kWe, generating an electricity income of £15/h, assuming a price of 6p/kWh or £0.06/kWh. (250 kWe x £0.06/kWh = £15/h)
Biomass input i250 kg/h
Char/ash output 7-10 kg/h
Condensate (water) 30 kg/h
Engine exhaust (within emissions limits) -
Electrical output (gross) 300 kWe
Electrical output (net) 250 – 275 kWe
Recoverable heat 450 – 600 kWth
Electricity production cost £30/MWh
ROO incentive £30/MWh

Production of Liquid fuels from Bio Mass
The major objective in bio-energy research is the production of liquid bio-fuels as substitutes for crude oil products. The three main approaches, treated in this section, could hardly be more different. The first is thermo-chemistry, which might be described as careful cookery. Second, is synthesis, which can be described as break down and start over again. The third is fermentation which is familiar to brewers and vintners for centuries. A good example would be the brandy trade in South Africa which is such an underrated process.

PYROLYSIS TO PRODUCE BIO-OIL
The method involves heating the bio-material with a carefully controlled air supply. It must not burn, of course, and as the aim is a liquid product, gasification must be minimised. The resulting reactions are complex and hard to predict, giving a range of oils, acids, water, solid char and uncondensed gasses, depending on the feedstock and operating conditions. The product, bio-oil, usually has about half the energy content of crude oil, and contains acid contaminants that must be removed. Variations on the basic process include solvolysis, the use of organic solvents at 200 - 300 °C to dissolve the solids into an oil-like product, and fast pyrolysis, requiring temperatures of 500 – 1300 °C and high pressures (50 – 150 atmospheres).
SYNTHESIZING LIQUID FUELS
The first stage in the synthesis is a shift reaction, to adjust the proportions of H2 and CO to the ratio required in the desired product. Methanol, for instance, is CH3OH and therefore needs two H2 molecules for each CO, a hydrogen-to carbon monoxide ratio of 2:1. In the Fischer-Tropsch process the two components are passed over a suitable catalyst at high temperature and pressure, and the product, initially formed as a gas, is condensed.
FERMENTATION TO PRODUCE ETHANOL
Fermentation is an anaerobic biological process in which sugars (C6H12O6) are converted to alcohol by the action of micro-organisms, usually yeast. The required product, ethanol (C2H5OH), is separated from other components by distillation. Unlike methanol, ethanol cannot simply substitute for petrol, but it can be used as a gasoline extender in gasohol, which is petrol containing 26% ethanol. The liquid resulting from fermentation contains about 10% ethanol, which is distilled off. The complete process requires a considerable heat input, usually supplied by crop residues. Brazil’s Pro-Alcool programme, producing ethanol from sugar residues, is the world’s largest commercial biomass system.
VEGETABLE OILS TO BIO-DIESEL
Vegetable oils are quite different from liquid fuels. They occur naturally in the seeds of many plants, and are extracted by crushing. Their energy content of 37 – 39 GJ/t is only a little less than that of diesel (about 42 GJ/t). They can be burned directly in diesel engines, either pure or blended with diesel fuel, but incomplete combustion is a problem, leading to carbon build-up in the cylinders, and conversion of the vegetable oils to bio-diesel is preferred. There are reports that in 2002 UK drivers were mixing vegetable oil from their local supermarkets with their diesel fuel. This is illegal – unless they take care to pay the tax – and may harm the engine. [Source: Renewable Energy, Second edition] 
|